【中国耐火材料网】
长期以来,受“有风就有铁”高强度冶炼思想的影响,一些高炉工艺配套不合理,导致送风系统和煤气处理系统能力富余太多,浪费严重;一些高炉结构设计不合理,导致寿命短,吨铁折旧费用高;一些高炉指标欠佳,能耗过高,导致吨铁成本过高;一些高炉工艺选择不当,导致生产维护成本高;一些高炉建设时技术不成熟,导致环保不达标。以上种种缺陷,带来很大的成本压力和环境压力,严重影响到钢企的市场竞争力。
针对以上问题,从设计技术的角度出发,可以通过挖掘原配套系统的潜力,采用合理炉型、可靠薄壁本体结构、高效节能冷却系统、高风温顶燃式热风炉、环保底滤水渣工艺及环保节能物料转运等技术,实现高炉炼铁的升级改造,确保高炉的高效、低耗、长寿和环保,达到降本增效、提升市场竞争力的目的。
优化炉型,提升高炉生产指标
长期以来,一些高炉因利用系数高就被认为效率高、技术水平高,从而得到众多钢铁企业的青睐。但实际上利用系数过高的高炉(尤其是部分中小高炉)普遍能耗高、吨铁成本较高。尤其是在目前的微利时代,这些高炉的缺陷逐渐凸显出来,甚至被贴上落后产能的标签。
优化炉型,选择合适的单位炉缸面积工作炉容(Vw/A)。高炉的生产指标不仅与原燃料条件和操作制度息息相关,而且与高炉炉型有密切的关系。为什么一些高炉尤其是中小高炉容易强化冶炼、产量高,但能耗较高,其根本原因在于单位炉缸面积对应的工作炉容偏小。
炉缸面积越大,燃烧燃料越多,煤气量就越大,产量也会相应增加。但是单位炉缸面积对应的工作炉容(Vw/A)与煤气在炉内的停留时间是密切相关的,它直接影响到煤气利用率。据统计,经济技术指标较好的高炉空塔炉缸煤气流速或者炉腹煤气指数ν为58m/min~66m/min,工作容积内煤气平均压力也相对稳定。要保持煤气在炉内足够的停留时间,必须有合理的Vw/A范围。由于中小高炉工作容积内煤气平均压力较小,Vw/A应该更大,而不是现在中小高炉比大高炉小得多的状态。当然煤气停留时间也不宜过长,在炉内6s~7s时,煤气基本完成了自身热能与化学能的传导,因此需要一个合理经济的Vw/A。
炉型优化改造投资并不高,并可适当挖掘原工艺潜力。高炉工艺流程中,高炉本体所占总投资的比例并不高,大约10%左右,高炉其他约90%的投资都是与产量挂钩的,跟高炉本体大一点、小一点关系不大。假设高炉不以提高产量为目的,仅为了改善生产指标,适当增加工作炉容100m3,其投资并不是增加3000万元(假定按照30万元/立方米炉容计算),而是只增加300万元或者更低,因为炉缸的投资大于炉腹及以上部位。如果将厚壁高炉改造成薄壁高炉,工作容积增加,投资反而下降。
如果适当增加炉容,降低冶炼强度和利用系数,提高煤气利用率,那么假设燃料比降低10kg/t,1000m3级高炉每年就节省近1000万元,仅半年就可以收回增加工作炉容的投资,今后每年增加1000万元的利润。
淘汰部分落后高炉,适当增加改造高炉的容积,尤其是适当扩大工作容积,选择合适的Vw/A,保证适宜的煤气流速和足够的炉内停留时间,提高煤气利用率,吨铁耗风量及煤气产生量都会相应减少。同时,挖掘送风和煤气处理系统的潜力,可以提高高炉产量,降低燃料比,降低吨铁成本,真正达到高产低耗,实现提升竞争力的改造目的。
采用先进可靠技术,延长高炉寿命
目前,我国高炉平均寿命与国际先进水平相比,有5年~10年的差距,究其原因,设计、操作、维护等方面均存在一些问题。近年来,炼铁技术飞速发展,如果不运用这些技术成果,仍然采用已经落后淘汰的技术对高炉进行原样大修,结果就会导致生产指标不能改善,吨铁成本仍然居高不下,损失巨大。
高炉长寿的关键在炉缸,炉缸的可靠性决定了一代炉役的长寿。炉缸寿命主要取决于炉墙结构是否合理、冷却能力是否足够及冷却能力是否得到充分的发挥等。
合理的薄壁炉衬结构。高炉改造,可以采用薄壁炉衬结构,适当增加炉腰直径,缩小炉腹角和炉身角,调整合适的Vw/A。采用密排水管的球墨铸铁冷却壁、钢冷却壁,甚至铜冷却壁,并满镶砖,以确保炉腹及以上炉墙的寿命。薄壁高炉并不是为了节省耐材、降低投资,而是将厚壁高炉经火法修正后,指标较好时期的内型在一代炉龄中固定下来,使得高炉在整个一代炉龄中都能保持高效低耗状态运行。要强调的是,薄壁高炉不能沿用厚壁高炉内型简单地将冷却壁热面推移到厚壁内型线位置的做法。那样既不能获得较好的生产指标,又会导致冷却壁过早破损,致使高炉短寿。
合理的炉缸结构。这主要包括以下6个方面的内容:一是采用斜炉缸结构,二是稳定且密封的陶瓷杯结构,三是提升碳砖及捣打料质量,四是适宜的风口、铁口设计,五是健全的监测系统,六是合理的烘炉制度。
高效节能的冷却系统。同种材质和工艺的冷却壁,管壁温度和热面温度都可以看作一定热流强度条件下冷却壁的冷却能力。温度越低,冷却壁冷却能力越强。冷却能力与管径、水量、水速以及比表面积,可以通过对3种型式炉缸铸铁冷却壁的对比看出其关系,如表1和图1。由表1和图1可以看出,采用小管径密排设计的冷却壁换热能力比大管径的要好,而不是水管越大、水量越大,冷却能力就越强。小而密的冷却水管布置的优点在于:可以提高冷却能力;降低冷却壁热面温度和对炉墙冷却的不均匀性,降低自身热应力,延长使用寿命;减少供水量,降低运行成本;减薄冷却壁,降低投资。
炉腹至炉身下部区域,可采用组合式冷却壁。其近年来在一些高炉上已得到成功应用,即在铸铁冷却壁热面部分燕尾槽内插装铜冷却条,提高铸铁冷却壁的冷却强度。铜冷却条作为渣皮“锚固钉”,使得冷却壁热面容易形成更加稳固的渣皮保护层。组合式冷却壁既具有易结渣皮寿命长的优点,又克服了铜冷却壁冷却过度造成渣皮太厚,继而频繁脱落给高炉带来的操作问题,同时投资较铜冷却壁大大降低。
高效的传热体系。尽管炉缸采用合理的结构、高强度的冷却系统,但如果炉墙有间隙,传热系统遭到破坏,耐材不能得到有效的冷却,炉缸安全仍然面临严重威胁。
由于耐材和炉壳膨胀很难同步,如果冷却壁和碳砖之间捣打料没有捣实,或者捣打料和碳砖有质量问题,冷却壁和耐材之间出现气隙就在所难免。在气隙存在的情况下,传热体系一旦遭到破坏,耐材就不能得到有效的冷却。要想解决这个问题,须要从冷却壁的安装结构入手。
按照常规设计,冷却壁是固定在炉壳上的,炉壳膨胀和冷却壁完全同步。而现在很多工程采用“无间隙冷却结构”专利技术,将冷却壁挂在炉壳上,设置排斥设施(如弹簧),通过排斥设施的反力,将冷却壁推向耐材,保证冷却壁在任何时候都与耐材紧密接触,充分发挥其冷却作用。“无间隙冷却结构”技术安装冷却壁时,将冷却壁固定在炉壳上,待碳砖砌筑,宽缝捣料后,适当松开螺母,再焊接封罩,可将冷却壁固定销、灌浆孔和“无间隙冷却结构”统一在一套设备中。
应用节能环保技术,提升竞争力
通过高炉改造,采用高温节能的旋切式顶燃式热风炉、环保底滤炉渣处理工艺、环保节能的卸料车和转载技术等高效、节能、环保技术,可以实现高炉炼铁节能减排、改善环境、提升竞争力的目标。
超高风温热风炉技术。提高高炉鼓风温度,不仅可以降低高炉冶炼的燃料消耗,而且有利于增加喷煤量,降低焦比,对于降低吨铁能耗和生产成本的效果是明显的。近年来,很多高炉入炉风温虽然有所提高,但与先进高炉1250℃左右的风温相比还是有差距的。
在高炉升级改造中,提高风温一般可以采取以下措施:一是将内燃式热风炉改造为旋切式顶燃式热风炉。二是提高废气温度,既能提高热风炉蓄热量,强化换热,又能提高煤气、空气预热后温度,也不增加运行成本,是提高送风温度的最佳措施。改善炉箅子的材质,优化支撑结构,使得炉箅子和支柱能够承受450℃甚至500℃以上的废气温度。三是改进混风方式,将混风管接至助燃空气支管,从燃烧器助燃空气喷口进入热风炉,根据热风出口温度的变化调节混风量。四是改进热风管系结构,采用低应力热风管系。
环保底滤技术。环保底滤高炉炉渣处理技术是一种经济、环保、省地的新型炉渣处理新工艺。环保底滤工艺技术有以下特点:一是蒸汽集中排放,无热水池,及时抽干过滤池,实现无水过滤,炉前和过滤区域无蒸汽,环境好。二是过滤池应用渗透过滤工艺,渣水分离彻底,过滤后渣中含水量低于0.12t/t渣,同时,渣池具有暂时储存功能。三是冷水冲渣,抓渣时过滤池内无冲渣水,显著减少蒸汽排放。四是过滤后的循环水中悬浮物含量低于30mg/m3,系统管道、阀门、水泵等几乎无磨损,过滤系统无运转设备,安全性和作业率高。清水泵电能消耗低,节能效果明显。五是过滤池过滤,抓渣采用桥式抓斗起重机,设备少,故障率低,作业安全、可靠。六是通过提高过滤速度,过滤池面积较常规底滤工艺减少一半;总的占地面积和冷水INBA(因巴法)相当,约650㎡(不含皮带)。七是一次性投资及运营成本低。环保底滤与转鼓法工艺的比较见表2。
环保矿焦槽技术。矿焦槽系统产生的大量粉尘,对环境及工人健康造成严重危害,因此,建议在矿焦槽系统设计中,采用环保卸料车。此外新型高效、节能、环保的原料运输及转载系统,可降低矿焦槽系统除尘能耗,减少环境污染。
现阶段开发的环保卸料车将卸料管和除尘管道分开,减小了除尘通风的阻力,气流顺畅,同时避免了皮带头轮空隙的漏风,最大程度地改善了除尘效果。
新型高效、节能、环保的物料运输及转载系统通过软件模拟设计出控流曲线溜槽,降低了料流速度,减少了成品物料的破损量,减少了粉尘量并减弱了粉尘气流。在除尘密封方面,该系统通过在皮带机头部采用升降式静电吸尘挡帘,采用高效的新型双层密封自降尘导料槽,以及在导料槽系统上增加粉尘阻尼减压器等措施,降低导料槽落料点的风能,降低气压,降低风速,进一步自降尘和降低除尘风量。矿焦槽系统槽下皮带数量多,每条皮带的下料点多且相对集中。新型转载系统适合于几个下料点集中除尘,除尘风量相应降低,环保效果明显改善,运行成本大幅度下降。
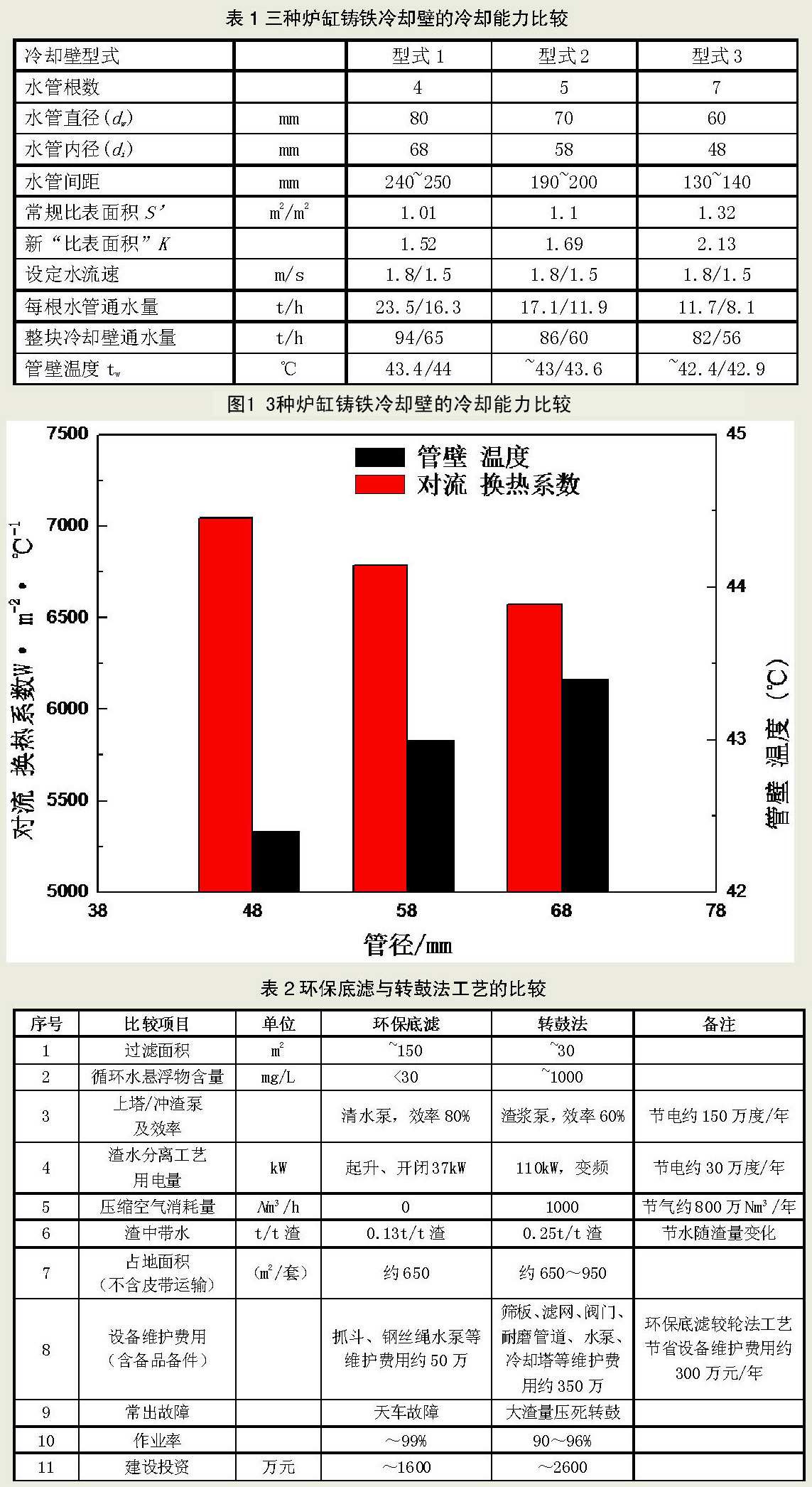
(来源:中国冶金报)